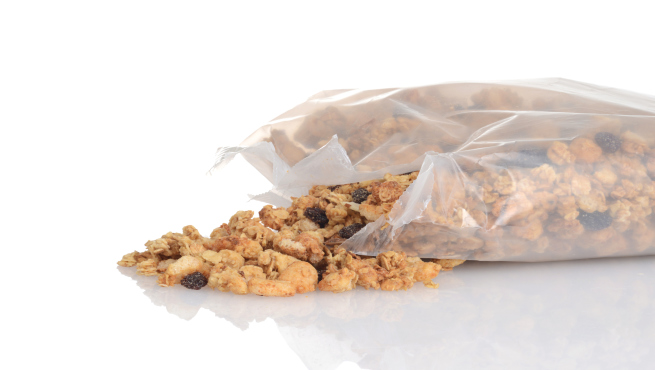
Have you ever heard the saying, “knowledge is power?” It’s a common idiom often applied to countless topics, including engineered films. But, for today, the focus will be specifically on barrier films.
Sure, technicians and formulators know barrier films well; it’s a big part of their job. But what about those responsible for buying engineered films? Sure, they may have the order in hand and a general idea of what they want, but do they understand the differences between barrier types? Do they know the properties of the materials used in their formulation?
It’s a knowledge gap that IEF has seen before, and if knowledge is indeed power, we want to empower your sales and procurement teams with a better understanding of how to choose between barrier films to help keep your product fresh and shelf-stable.
A tale of two barriers
The first question to ask when sourcing engineered barrier film is simple yet obvious:
“What do I want to keep out?”
For Steve Brzostowicz, Technical Director at IEF, this leaves you with two options.
“When you’re talking about barrier films, there’s two different types. Often, the application will determine the type of barrier you go with,” said Brzostowicz. “If you’re looking for barrier film for pre-packaged cheeses and meats, you need an oxygen/vapor barrier. If you’re looking to keep dry goods from going stale too soon, pick a moisture barrier.”
While it seems pretty straight forward, knowing the type of barrier film your product requires has far reaching implications that go beyond simply having the right formulation.
“Getting the right barrier film for your application is about more than just protecting your product. It’s going to help keep your product fresh and curtail food waste,” said Brzostowicz. “An oxygen barrier is going to help preserve the quality and flavor of your product. A moisture barrier, on the other hand, will help stop your product from going stale prematurely and can have a dramatic effect depending on your product and the method used to package it,” he said.
Either way, if you choose the wrong film barrier, the product’s shelf life will take a hit, which just means more needless food waste.
Materials matter
Just as barrier films are formulated for specific tasks, the raw materials in these barriers play a major role in how they function.
“Looking at the components needed to make these barrier films, we often talk about three specific materials,” said Brzostowicz. “High-density polyethylene or polypropylene, ethyl vinyl alcohol (EVOH) and nylon.”
But how do these materials compare when it comes to performance? Here’s a breakdown:
- High Density Polyethylene or Polypropylene - Ideal for moisture barrier formulations. These films offer better oxygen barrier properties compared to low-density polyethylene or polypropylene, but are not as effective as nylon or EVOH for oxygen permeability.
- Nylon - Suitable for oxygen barrier formulations. Outperforms high-density polyethylene or polypropylene but is not as effective as EVOH. Additionally, nylon provides strength and durability to barrier films.
- EVOH - Ideal for oxygen barrier formulations. EVOH outperforms high-density polyethylene or polypropylene and nylon. This material can be brittle and is often used in the core of barrier films.
Build-a-barrier: Formulating for your product
With a better understanding of barrier types and the materials that make them, it’s time to understand how these all come together to form the right barrier for your product.
“Whatever barrier you’re looking for, the formulation you end up with will have some combination of these three materials,” said Brzostowicz. “Typically, polyethylene will be used least often as a skin. EVOH is always placed in the core of the formulation, because it’s very moisture sensitive. Nylon can be placed either in the core or on the outside skin, especially if heat resistance is specified.”
In practice, its best to combine for specialty products that need both oxygen and moisture protection. For Brzostowicz, his go-to cereal also happens to be his go-to example when describing such formulations.
“Cereal that contains grains, fruits and nuts is a great example of a barrier film application that’s going to need both moisture and oxygen barrier properties,” he said.
"An application like this requires a film with high density polyethylene layers to protect the grains and granola from becoming stale. It also needs EVOH or nylon layers to stop the natural oils from the nuts seeping through the barrier and damaging the packaging.”
When it comes to helping current and potential customers find their ideal barrier film, it always comes back to knowing your product to determine the best option.
“Sometimes we get technically-knowledgeable customers who know exactly what they’re looking for and ask for our recommendations,” said Brzostowicz. “Other times, we get potential customers who aren’t entirely sure what they need. That’s when we have the discussion about their industry and our experience creating barrier films for that industry. Conversations like this let us make better-informed recommendations, which in turn allows us to help put them in a position to make an educated buying decision.”
Now that you’re well versed in barrier films, get in touch with our technical experts here and let us know how we can help you formulate your next barrier film.
Published November 2018